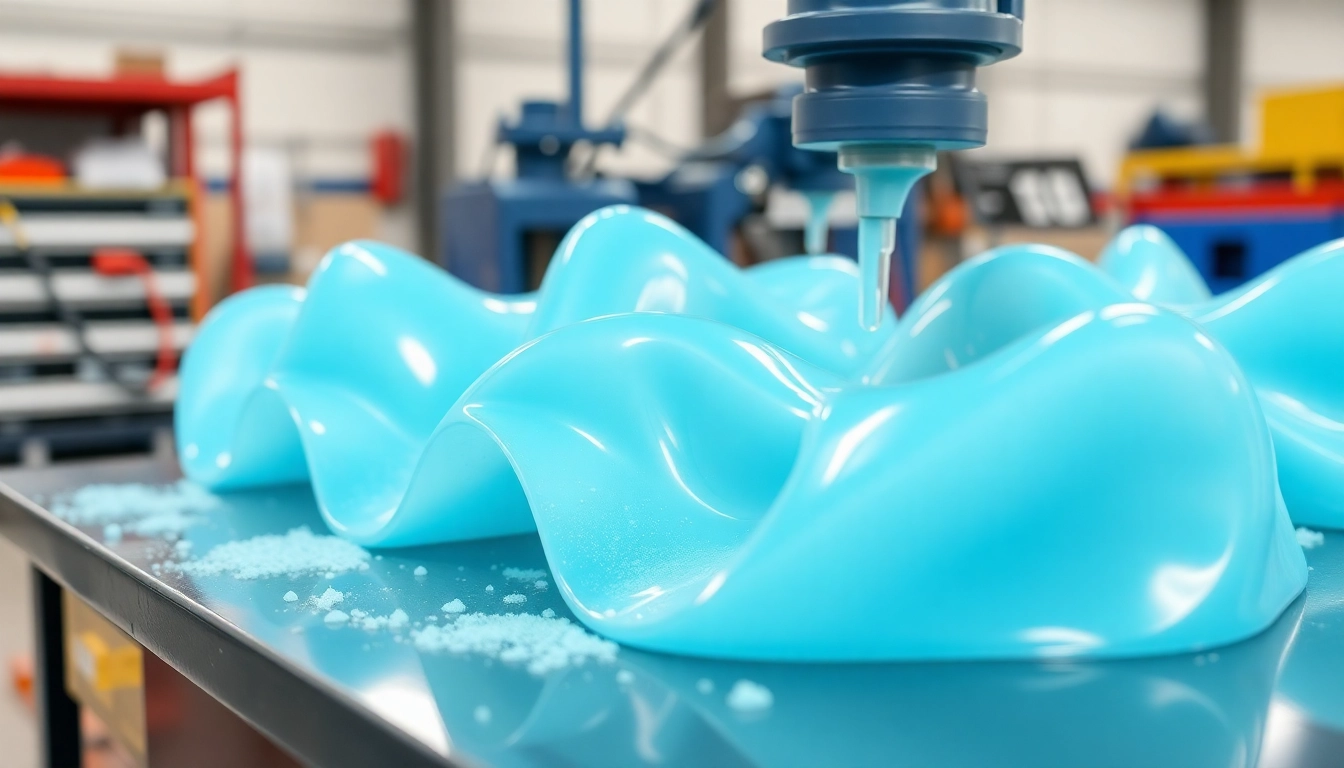
Introduction to Blow Molding Technologies
In the ever-evolving world of manufacturing, Blow Molding Machine Supplier stands as a pivotal player, aiding a range of industries in the creation of complex plastic products. This article explores blow molding technologies extensively, offering insights into selecting the right supplier and understanding the advantages of advanced machinery. As we journey through various types of blow molding processes, their applications, and emerging trends, you’ll gain a comprehensive understanding of the sector.
What is Blow Molding?
Blow molding is a manufacturing process used to create hollow plastic parts. The process begins by heating and melting the plastic to a specific temperature. This molten plastic is then shaped into a parison, which is a tube-like piece. Once formed, the parison is inflated by air within a mold, allowing it to adopt the shape of the mold cavity. This method is pivotal for producing a variety of products, including bottles, containers, and other complex shapes. It’s particularly valued for its efficiency, scalability, and cost-effectiveness, making it ideal for mass production.
Types of Blow Molding Processes
There are three primary types of blow molding processes: extrusion blow molding (EBM), injection blow molding (IBM), and stretch blow molding (SBM).
- Extrusion Blow Molding (EBM): This technique involves extruding a plastic parison, which is then enclosed in a mold to create a hollow object. It offers flexibility in terms of design and is highly efficient for large-scale production.
- Injection Blow Molding (IBM): In this process, plastic is first injected into a mold to form a preform, which is then transferred to a blow mold where it is inflated to achieve the final shape. IBM is often used for smaller, more intricate items, such as pharmaceutical containers.
- Stretch Blow Molding (SBM): This method involves stretching the preform both radially and axially during the blow molding process. It’s particularly suited for producing bottles with high clarity and strength, such as those used in beverage packaging.
Applications in Industries
Blow molding technology finds application across various sectors. The most prominent industries include:
- Food and Beverage: The production of bottles and containers for water, soft drinks, and other beverages.
- Pharmaceutical: Creating drug delivery systems and containers that require sterility.
- Household Products: Development of items like household cleaners and toiletries.
- Automotive: Manufacturing of components like fuel tanks and dashboards.
Choosing the Right Blow Molding Machine Supplier
Selecting a reliable blow molding machine supplier is critical to ensuring that your production runs smoothly and efficiently. Various factors come into play during this evaluation.
Evaluating Supplier Reputation
The reputation of a blow molding machine supplier can significantly impact your operation. Researching customer reviews, seeking testimonials, and analyzing their history in the industry can provide insight into their reliability and service quality. Established suppliers reap the benefits of human capital and technical knowledge accumulated over years, ensuring they remain at the forefront of innovation and customer satisfaction.
Key Features to Look For
When assessing potential suppliers, consider the following critical features:
- Machine Versatility: The ability of the machine to handle different types of plastics and production volumes.
- Energy Efficiency: Machines that reduce energy consumption while maximizing output are highly beneficial in terms of operating costs.
- Technical Support: Reliable customer service and support, especially regarding maintenance and troubleshooting, are essential.
- Innovation: A supplier that continually invests in research and development can provide access to cutting-edge technologies.
Cost Considerations and Budgeting
The cost of purchasing a blow molding machine varies widely based on its type, size, and features. It’s crucial to establish a budget that considers not only the initial purchase price but also long-term operational costs, maintenance charges, and potential downtimes. A comprehensive cost analysis allows businesses to make informed decisions that align with their financial strategy, ensuring sustainability in operations.
Benefits of Advanced Blow Molding Machinery
Investing in advanced blow molding machinery brings multiple benefits that can enhance production efficiency and product quality.
Efficiency and Productivity Enhancements
Modern blow molding machines incorporate automation and sophisticated controls that streamline production processes, reducing cycle times and minimizing waste. These efficiency gains are critical for maintaining profitability in a competitive market.
Quality Assurance in Production
Advanced machines often come with integrated quality control systems that monitor production parameters in real-time. This ensures any deviations from product specifications are promptly addressed, improving the overall quality and consistency of produced items.
Environmental Impact and Sustainability
With rising environmental concerns, many advanced blow molding machines are designed to optimize resource use, facilitating recycling and reducing emissions. Suppliers that prioritize sustainability can provide machines that feature closed-loop systems and utilize biodegradable materials, contributing to a greener manufacturing process.
Top Blow Molding Machine Suppliers in the Market
Identifying leading blow molding machine suppliers can significantly influence production quality and operational efficiency. Here, we analyze top-rated companies in the industry based on various metrics.
Comparative Analysis of Leading Brands
Notable manufacturers like Uniloy and Parker have established themselves as market leaders, thanks to their innovation and commitment to quality. Uniloy leads with a variety of blow molding technologies, while Parker’s extensive experience and global reach make it a preferred choice for many. Comparing the unique selling propositions of each brand is essential for selecting the right supplier for your specific needs.
User Testimonials and Case Studies
Examining case studies and testimonials from other manufacturers can provide excellent insight into the capabilities of various suppliers. For example, a company utilizing Parker’s extrusion blow molding technology reported a 30% increase in production efficiency alongside a significant decrease in operational costs. Such real-world examples can validate the claims made by suppliers and influence decision-making.
Geographical Presence and Support
The geographical presence of a supplier can impact service delivery times and support availability. Companies with a broad network are usually better positioned to provide timely maintenance and technical assistance, crucial for minimizing downtime.
Future Trends in Blow Molding Technology
The world of blow molding technology is continuously evolving. Being aware of upcoming trends can help businesses prepare for future challenges and opportunities.
Innovations in Machine Design
Emerging designs focus on modularity and scalability, allowing manufacturers to easily upgrade their systems as demand changes. Innovations in materials, such as the use of lighter yet more durable plastics, are also shaping the future of blow molding.
Automation and Smart Manufacturing
As Industry 4.0 takes hold, automation within blow molding processes is expected to rise. Smart machines with IoT capabilities will facilitate better data collection and analysis, driving efficiency and reducing operational costs.
Market Predictions and Growth Opportunities
The global blow molding market is projected to grow significantly in the coming years, driven by increasing demand in industries like food and beverage, healthcare, and automotive. Companies that adapt to changing consumer preferences and technological advancements are well-positioned to seize growth opportunities.