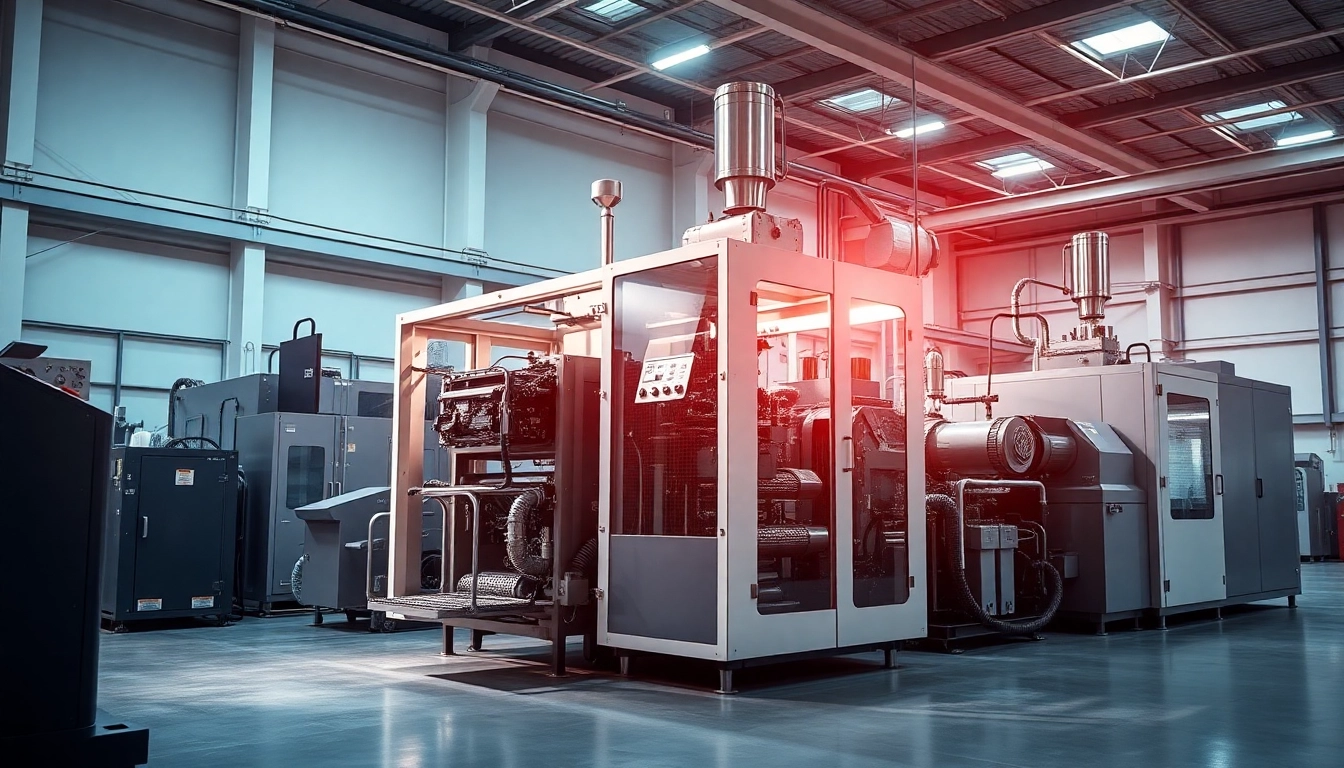
Why Choose a Quality Blow Molding Machine Supplier?
In the competitive landscape of plastic manufacturing, the selection of a reliable Blow Molding Machine Supplier can be pivotal to success. The right supplier not only provides the machines necessary for production but also ensures that the machines operate effectively and meet the specific needs of the business. Selecting a high-quality supplier translates into operational efficiency, reduced production costs, and improved product quality.
The Importance of Advanced Technology
The blow molding machine industry has experienced considerable technological developments over the years. Advanced technologies such as automation, smart sensors, and high-precision manufacturing processes enhance machine operation and reduce waste. Suppliers who offer cutting-edge technology provide their customers with machines that not only outperform but also have the potential to revolutionize production facilities. These advancements often lead to higher energy efficiency, better cycle times, and products that meet or exceed industry standards.
Evaluating Machine Efficiency and Performance
When assessing a blow molding machine supplier, it’s crucial to consider the efficiency and performance of their machines. This involves understanding the throughput, cycle times, and energy consumption rates of the machinery offered. High-efficiency machines contribute to a more streamlined production process, allowing for an increase in output with reduced operational costs. Suppliers who provide access to performance metrics and real-world usage data can help manufacturers evaluate the best fit for their production requirements.
Understanding Supplier Support and Services
Beyond the initial purchase, ongoing support and services from a blow molding machine supplier are critical. This includes maintenance services, access to spare parts, and technical support for troubleshooting during production downtime. Suppliers who emphasize customer service often develop long-term relationships with clients, fostering mutual growth and enhancing overall productivity.
Types of Blow Molding Machines
Blow molding machines come in several configurations, each suited to different applications and product specifications. Understanding the different types ensures that manufacturers select the right machine for their production goals.
Extrusion Blow Molding Machines: Features and Benefits
Extrusion blow molding (EBM) machines are widely used to create hollow plastic products. The process involves melting plastic and forming it into a parison, which is then inflated in a mold. EBM machines are known for their versatility, capable of producing a wide range of products such as containers, bottles, and tanks.
Some notable features and benefits include:
- High-volume production: Ideal for producing large runs of identical products.
- Cost-efficient: Reduces material waste through efficient use of plastic.
- Versatility: Various configurations can accommodate different product shapes and sizes.
Injection Blow Molding Machines: Advantages for Small Batches
Injection blow molding (IBM) machines combine injection molding and blow molding techniques, making them ideal for producing smaller batches of custom-designed products. This method allows for greater control over the wall thickness and allows for designs that require detailed aesthetic finishes.
Advantages of this type include:
- Precision: Offers tight tolerances for detailed components.
- High-quality surface finishes: Ideal for products with cosmetic requirements.
- Flexibility: Best suited for complex shapes and designs.
Stretch Blow Molding: Applications and Use Cases
Stretch blow molding is typically used for producing PET bottles, including soft drink and water containers. This process stretches the preform, creating a strong and lightweight final product that is resistant to pressure and provides excellent clarity.
Common applications include:
- Beverage containers: Ideal for carbonated soft drinks and juices.
- Pharmaceutical and cosmetic bottles: Provides a hygienic and visually appealing option for sensitive goods.
Cost Considerations When Selecting a Blow Molding Machine Supplier
Cost analysis is an essential aspect when choosing a blow molding machine supplier. While initial costs are significant, understanding long-term expenses is equally important to gauge the actual investment’s viability.
Understanding Initial Investment vs. Long-term ROI
The upfront cost of purchasing a blow molding machine can vary greatly depending on its type and capabilities. However, it’s vital to consider potential long-term returns on investment (ROI). Machines that are more efficient and require less maintenance can significantly offset initial costs over time through reduced operational expenses and increased output efficiency.
Maintenance Costs: What to Expect
Every blow molding machine will require ongoing maintenance to ensure optimal performance. Regular maintenance checks, prompt repair services, and the cost of replacement parts can add up over time. Selecting a supplier who provides transparent maintenance agreements or warranties can help manufacturers better anticipate and manage these potential costs.
Industry Pricing Trends
Understanding current industry pricing trends can aid manufacturers in making informed purchasing decisions. Factors influencing market prices include advancements in technology, the rise of eco-friendly materials, and shifts in supply chain dynamics. Engaging with a supplier who is well-informed about these trends can optimize negotiating power, allowing for better deals and terms.
Key Features to Look For in a Blow Molding Machine
When selecting a blow molding machine, features and capabilities can significantly influence production outcomes. Understanding which features matter the most allows for more informed purchasing decisions.
Automation and Control Systems
Advanced automation and control systems lead to greater efficiency and consistency in the production process. Features to consider include programmable logic controllers (PLCs) and human-machine interfaces (HMIs) that enhance operational oversight. Automation can reduce the need for labor-intensive processes, ultimately minimizing error rates and production costs.
Material Compatibility and Flexibility
The ability of a blow molding machine to work with various types of plastic resins expands production capabilities significantly. Suppliers should provide machines that are flexible enough to handle different materials, including biodegradable options, which are increasingly popular due to sustainability efforts across the industry.
Safety Features and Compliance
Ensuring operator safety while complying with industry regulations is a critical component of selecting a blow molding machine. Look for features such as emergency stop buttons, safety guards, and compliance with ISO standards relevant to blow molding operations. A machine that prioritizes operator safety helps reduce workplace incidents and can lower insurance costs.
Questions to Ask Your Blow Molding Machine Supplier
Prior to making a purchase, it’s essential to engage with the supplier through a series of well-considered questions. This dialogue can provide invaluable insight into how the supplier operates and what you can expect long-term.
What is the Lead Time for Delivery?
Understanding the lead time for delivery can help manufacturers plan their production schedules effectively. It’s crucial to ask about potential delays and how the supplier manages logistics to meet demand.
What Kind of Technical Support is Available?
Ask your supplier about the technical support options available post-purchase. This includes querying about response times for service calls, availability of remote diagnostics, and the comprehensiveness of the documentation provided for the machine.
Can I See a Demo of the Equipment?
Requesting a demonstration of the blow molding equipment can be instrumental in understanding its capabilities and operations. A live demo allows you to see the machine in action, evaluate its performance, and ask technical questions directly related to your production needs.