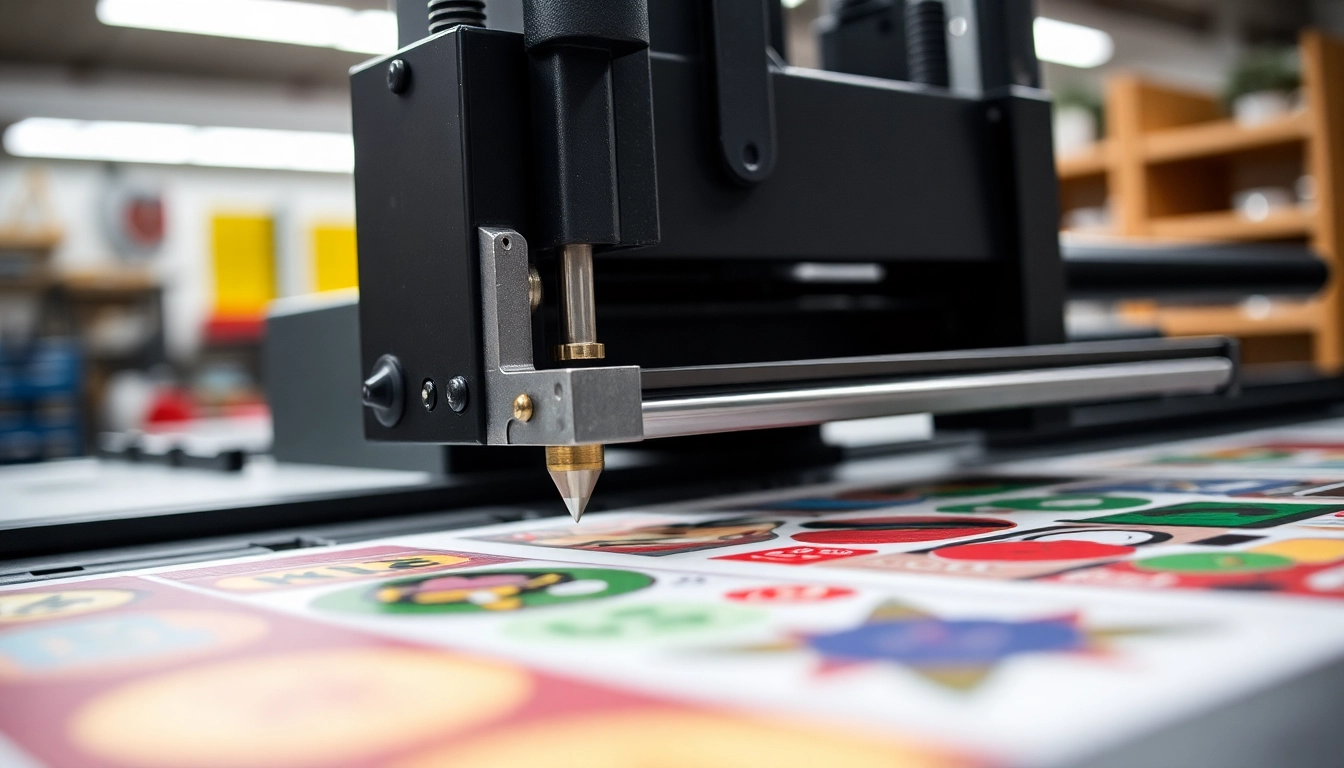
Understanding Precision Die Cutting
Definition and Basics of Precision Die Cutting
Precision die cutting is a manufacturing process used to cut or shape materials with extreme accuracy and consistency. This technique utilizes a die—a specialized tool designed for specific shapes and patterns—allowing manufacturers to produce custom parts efficiently. By ensuring that each cut is made with precision, businesses can achieve high-quality results that meet exact specifications. As a fundamental aspect in various industries, precision die cutting enables the transformation of flat materials, such as sheets and rolls, into intricately shaped components suitable for assembly or direct use in final products.
Materials Used in Precision Die Cutting
The versatility of precision die cutting stems from the variety of materials it accommodates. Common substrates include:
- Plastics: Used in various applications, from packaging to automotive parts.
- Foams: Essential in insulation and cushioning products.
- Metals: Thin sheets of metal can be die-cut for complex industrial components.
- Papers and Cardboards: Frequently used for packaging and promotional materials.
- Adhesive-backed materials: Allows for immediate application in assembly contexts.
These materials can be manipulated to create customizable components that fulfill specific functional and aesthetic requirements, expanding the possibilities for design and production.
The Importance of Precision in Die Cutting
Precision is paramount in die cutting for several reasons:
- Quality Assurance: High precision reduces waste, enhances consistency, and maintains the integrity of products.
- Cost-Efficiency: Accurate cuts minimize material loss and defects, which reduces overall production costs.
- Market Competitiveness: Businesses can offer unique designs and reliable products, influencing market reputation and consumer choice.
In industries where precision is essential, such as medical device manufacturing or automotive production, the need for stringent tolerances (often as tight as ±0.005 inches) commands a methodical approach incorporating advanced die cutting technologies.
Types of Precision Die Cutting Techniques
Flatbed Die Cutting Explained
Flatbed die cutting involves a hydraulic press that utilizes a flat die to cut or shape materials. As the press lowers, the die presses down on the substrate, producing clean cuts. This technique is often suited for thicker materials and those requiring precise shapes and intricate designs. Common applications of flatbed die cutting include:
- Packaging production for heavy-duty materials
- Creating custom gaskets
- Fabric cutting for apparel and upholstery
Understanding Rotary Die Cutting
In contrast, rotary die cutting employs a cylindrical die that rotates while the material moves through the machine. This method is well-suited for high-volume production due to its speed and efficiency. Rotary die cutting offers several benefits:
- Continuous cutting processes enhance throughput.
- Ideal for thinner materials such as films and foils.
- Can incorporate printing, laminating, and various finishing processes in a single run.
The technique is widely used in applications like labels, tags, and packaging, particularly when volume and speed are critical factors.
Choosing Between Rotary and Flatbed for Your Project
The choice between rotary and flatbed die cutting often depends on the specific requirements of a project. Factors to consider include:
- Material Thickness: Flatbed works better for thicker substrates, while rotary suits thinner dimensions.
- Production Volume: Rotary die cutting is more affordable at scale, making it favorable for mass-produced items.
- Design Complexity: Flatbed die cutting allows for intricate designs and custom shapes.
Ultimately, understanding the specific needs of a project will guide the decision-making process effectively.
Applications of Precision Die Cutting
Industrial Applications of Precision Die Cutting
In industrial settings, precision die cutting is pivotal in producing components that need to meet stringent tolerances for performance and safety. Key uses include:
- Automotive Parts: Many components, such as seals, spacers, and sound dampeners, require precision die cutting to ensure functionality and compatibility.
- Electronics: Precision cut parts for circuit boards, insulation, and locking mechanisms are critical for reliable performance.
- Construction: Die-cut insulation materials and gaskets enhance structural integrity and efficiency.
Use in Medical Industries
Precision die cutting is essential in the medical sector for producing components used in diagnostic devices, surgical instruments, and packaging for sterile products. With stringent regulations and the need for high-quality standards, die cutting helps in:
- Creating custom surgical templates and drapes.
- Manufacturing precise adhesive components for medical devices.
- Ensuring sterile packaging solutions that meet federal standards.
The ability to quickly produce small batches or high volumes of quality-controlled medical components underscores the critical role of precision die cutting in healthcare.
Applications in Consumer Products and Packaging
Consumer products benefit significantly from precision die cutting in various ways:
- Packaging: Custom packaging designs are created through precision die cutting, ensuring products fit snugly, are easily opened, and maintain integrity during transport.
- Labels and Tags: High-quality, versatile tags and labels can be designed with intricate shapes or cut-outs that enhance branding efforts.
- Promotional Items: Creative designs for posters, displays, and seasonal packaging are achieved with precision die cutting techniques.
These applications illustrate how die cutting can enhance not only the functional aspects of consumer goods but also their aesthetic appeal.
Best Practices for Effective Precision Die Cutting
Design Considerations for Die Cutting
Successful die cutting begins with effective design. Considerations must be made for:
- Material Properties: Understanding how different materials behave during cutting will influence the design process.
- Tolerances: Establishing the required tolerances ensures parts fit together correctly. Common tolerances range from ±0.005 to ±0.010 inches.
- Die Design: Custom dies should be designed to minimize material waste while maximizing production efficiency.
Quality Control Measures
In precision die cutting, maintaining quality is essential. Implementing stringent quality control measures includes:
- Regular Inspections: Conduct inspections throughout production to catch inconsistencies.
- Dimensional Testing: Utilize advanced tools to verify dimensions and tolerances.
- Traceability: Maintain records of materials and processes to identify and address quality issues swiftly.
Quality control safeguards product integrity and ensures compliance with industry standards, particularly in sensitive sectors like medical manufacturing.
Cost Efficiency Tips in Precision Die Cutting
To maximize the cost-effectiveness of precision die cutting, businesses can employ several strategies:
- Material Optimization: Designing die cuts to minimize scrap material can significantly reduce costs.
- Batch Production: Running large volumes of materials can spread costs and save on per-unit pricing.
- Investing in Automation: Incorporating automated processes can enhance speed and reduce labor costs over time.
These strategies pave the way for businesses to balance quality and efficiency, ultimately boosting profitability.
The Future of Precision Die Cutting Technology
Emerging Trends in Die Cutting Techniques
The future of precision die cutting is predicted to be influenced by numerous technological advancements, including:
- 3D Printing Integration: The merging of die cutting with additive manufacturing could lead to hybrid production techniques, offering even more design freedom.
- Smart Technologies: Implementation of IoT devices for real-time monitoring and adjustments during the die cutting process.
- Software Innovations: Improved design software enables better planning and simulation of die cutting processes before physical production starts.
These trends reflect a growing emphasis on innovation and efficiency within the manufacturing space.
Advancements in Die Cutting Machines
Modern die cutting machines are becoming more sophisticated. Key advancements include:
- Laser Technology: The integration of laser cutting technology allows for cleaner cuts and greater versatility.
- Quick-Change Dies: New designs enable faster die changes, reducing downtime and improving workflow efficiency.
- Increased Automation: Fully automated die cutting lines reduce labor costs and increase precision by minimizing human error.
These innovations will likely continue to shape the landscape of manufacturing, making it more efficient and responsive to market demands.
Environmental Considerations and Sustainability in Die Cutting
As industries become increasingly aware of their environmental impact, sustainability within precision die cutting is gaining attention. Companies are exploring approaches such as:
- Recyclable Materials: Selecting materials that are more sustainable, reducing environmental footprints.
- Waste Management: Implementing processes that minimize waste generation and promote recycling.
- Energy Efficiency: Opting for equipment that consumes less energy while maximizing production output.
By adopting sustainable practices, companies not only enhance their reputation but also contribute positively to environmental conservation efforts.