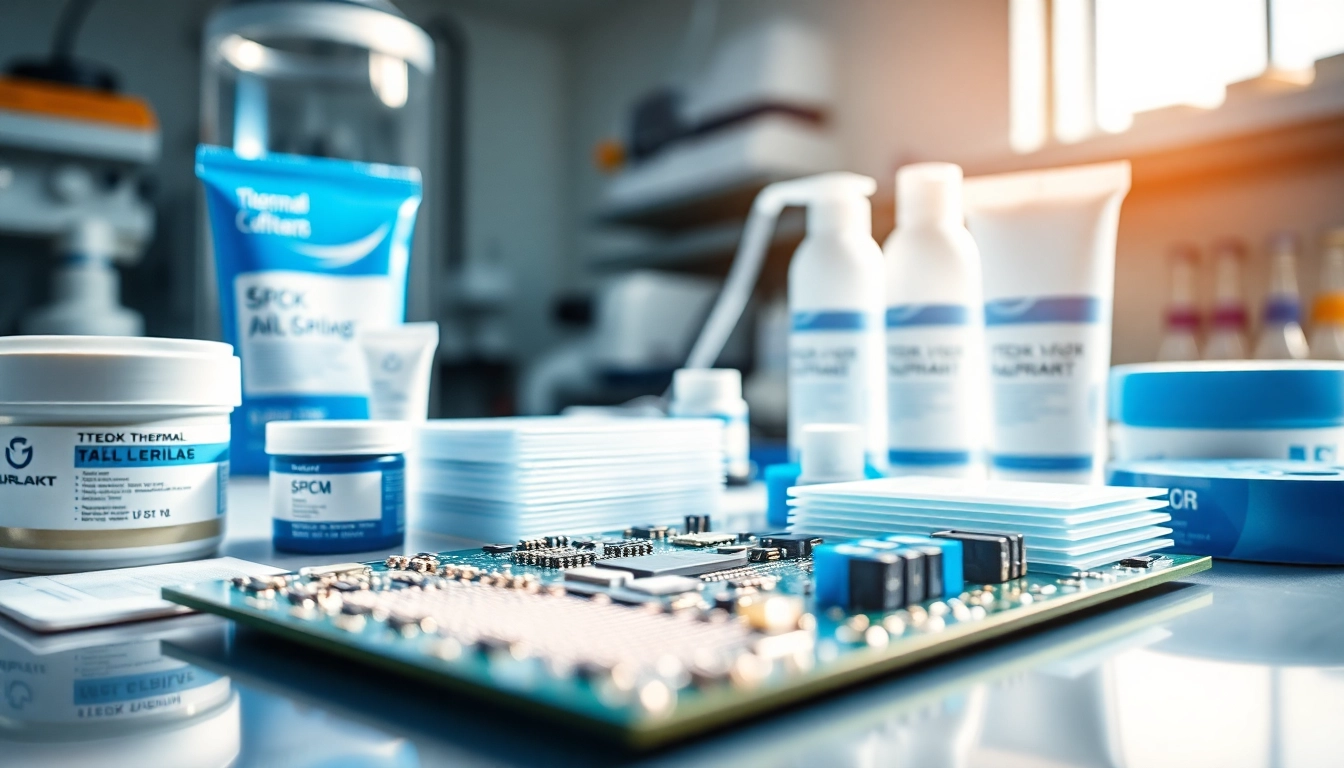
Introduction to Thermal Management Materials
In our ever-evolving technological landscape, the demand for effective heat management has never been more critical. Thermal management materials play a pivotal role in ensuring the reliability and efficiency of electronic devices. Thermal management materials encompass a diverse range of products designed to dissipate heat efficiently, preventing overheating and ensuring optimal performance. As electronic devices become more compact and powerful, understanding the nuances of thermal management materials is essential for manufacturers, engineers, and technicians alike.
What Are Thermal Management Materials?
Thermal management materials are specialized materials used in various applications to control heat transfer. The goal is to either dissipate heat generated by electronic components or insulate sensitive parts from excess temperatures. This includes everything from electronics in smartphones to servers in data centers, where the proper functioning of thermal management materials is integral to device longevity and performance.
Importance in Electronics Cooling
The importance of thermal management materials cannot be overstated, particularly in the world of electronics. As devices become increasingly smaller and more powerful, they generate significant amounts of heat. Excessive heat can lead to system failures, reduced efficiency, and shortened lifespans for components. Thus, employing quality thermal management solutions can result in enhanced device reliability, improved performance, and ultimately, lower costs due to reduced maintenance and replacement frequencies.
Common Applications
Thermal management materials are utilized in a wide variety of applications across numerous industries. Some of the most common applications include:
- Consumer Electronics: Smartphones, tablets, and laptops require efficient thermal management systems to operate under heavy workloads without overheating.
- Automotive: Electric vehicles (EVs) and hybrids utilize thermal management materials to cool batteries and power electronics effectively.
- Telecommunications: Telecom equipment produces heat; thus, effective thermal management ensures optimal performance in telecom facilities and data centers.
- Aerospace: Thermal management is vital in aerospace applications, where electronic systems must operate under extreme temperature variations.
Types of Thermal Management Materials
There are several types of thermal management materials, each designed to meet specific needs and requirements. Below are some of the most widely used types:
Thermal Interface Materials (TIMs)
Thermal Interface Materials are substances that enhance the conduction of heat between two surfaces. TIMs fill any microscopic air gaps between these surfaces, which can act as insulators and hinder heat transfer. Examples of TIMs include:
- Thermal Greases: These are viscous compounds applied between components, improving thermal conductivity and minimizing thermal resistance.
- Thermal Pads: These pre-formed materials provide excellent thermal conductivity while also serving as a cushioning agent for device components.
- Phase Change Materials (PCMs): These materials change their phase (solid to liquid) at specific temperatures to absorb and release heat efficiently.
Thermal Pads and Gels
Thermal pads and gels are crucial in heat dissipation applications due to their conformability and effectiveness. They are easy to apply and can cover large surface areas for improved contact. Here are some key points:
- Thermal Pads: Made from silicone or other polymer compositions, these pads provide a combination of thermal conductivity and compressibility. They adapt to the surface contours of heat-generating components, ensuring an effective thermal interface.
- Thermal Gels: These are often used when a softer interface material is needed. Thermal gels offer a higher thermal performance than conventional greases and can fill uneven surfaces more effectively.
Conductive Adhesives
Conductive adhesives not only bond components but also facilitate heat transfer. They typically contain conductive fillers like silver or carbon and are useful in specific applications where mechanical strength and heat transfer capability are required. Key characteristics include:
- Electrical Conductivity: Many conductive adhesives offer excellent electrical conductivity, crucial for electronic assembly.
- Heat Resistance: These adhesives can endure high temperatures, making them suitable for applications involving substantial heat generation.
Best Practices for Selecting Thermal Management Solutions
Selecting the right thermal management material is critical to the overall effectiveness of an electronic assembly. Below are best practices to consider when selecting thermal management solutions:
Understanding Thermal Conductivity
Thermal conductivity is a measure of a material’s ability to conduct heat. Materials with high thermal conductivity, such as metals, are typically preferred for thermal management applications. When comparing materials, look for:
- The thermal conductivity rating (often expressed in Watts per meter-Kelvin, W/mK)
- Any specifications related to thermal resistance and performance across varying temperatures
Factors Influencing Material Choice
Several factors can influence the choice of thermal management materials, including:
- Application Requirements: The specific thermal requirements and constraints of an application should guide material selection.
- Environmental Conditions: Consider factors such as humidity, exposure to chemicals, and whether the material needs to operate in an extreme environment.
- Cost: Evaluate the trade-off between performance and cost-efficiency for each potential solution.
Application-Specific Recommendations
Different applications have different needs. It is essential to tailor the thermal management solution to the specifics of the application. For example:
- In electronics, tightly packed systems may benefit more from thermal pads and gels to ensure maximum coverage and conductance.
- In automotive applications, users might prefer conductive adhesives that provide bonding in addition to thermal management.
Challenges in Thermal Management
Despite advances in thermal management materials, various challenges still exist. Recognizing these challenges allows for proactive problem-solving:
Common Problems in Electronics Cooling
Overheating remains a primary concern in electronics cooling, leading to failures and reduced efficiency due to thermal management issues. Some common problems include:
- Inadequate heat dissipation from surface areas resulting in localized overheating.
- Improper choice of materials leading to increased thermal resistance.
- Degradation or failure of thermal management materials due to harsh environmental conditions.
Preventive Strategies
A proactive approach to prevent thermal management issues should include:
- Regularly assessing thermal interface materials for wear and tear, especially in high-use environments.
- Implementing proper surface preparation to maximize the effectiveness of TIMs.
- Conducting extensive thermal simulations during the design phase to anticipate potential cooling issues.
Innovations in Thermal Technology
The thermal management materials landscape is constantly evolving. Recent innovations include:
- Nano-Enhanced Materials: These materials harness nanotechnology to significantly improve thermal conductivity.
- Sustainable Options: The shift towards environmentally friendly products is gaining traction, with manufacturers exploring bio-based thermal materials.
Measuring Performance of Thermal Management Materials
Once thermal management materials are selected and applied, measuring their performance is crucial to ensuring they are functioning as intended. Here are some key metrics and methods:
Key Metrics to Consider
When assessing thermal management materials, consider the following metrics:
- Thermal conductivity (W/mK) indicating the material’s efficiency at conducting heat.
- Thermal resistance (°C/W) which illustrates the resistance the material provides against heat flow.
- Long-term reliability and stability under expected environmental conditions.
Testing and Validation Methods
To validate the performance of thermal management materials, manufacturers often employ testing methods such as:
- Transient Plane Source (TPS): This method provides accurate thermal conductivity measurements and is ideal for solid materials.
- Thermal Imaging: This non-intrusive technique uses infrared cameras to visualize temperature distributions and identify hotspots.
Future Trends and Developments
The realm of thermal management continues to advance, with several key trends emerging:
- Increased integration of smart materials that respond to temperature changes dynamically.
- The continued focus on developing lighter, thinner materials without compromising performance for applications in consumer electronics and automotive sectors.